Let the light in - Glass railing systems enhance daylighting
Eve Zhou
Andrew Chatfield
2017-08-07 11:43:06
Everywhere you look today, architects are leveraging glass for daylighting purposes to allow the right amount of light into a building. But while much of the attention centers on the façade, interior spaces leveraging glass are just as critical to the introduction of natural light into the building environment. For interior space in particular, glass railing systems for stairways and balconies play a key role in letting the light in. And that means opportunities for glaziers with glass railings.
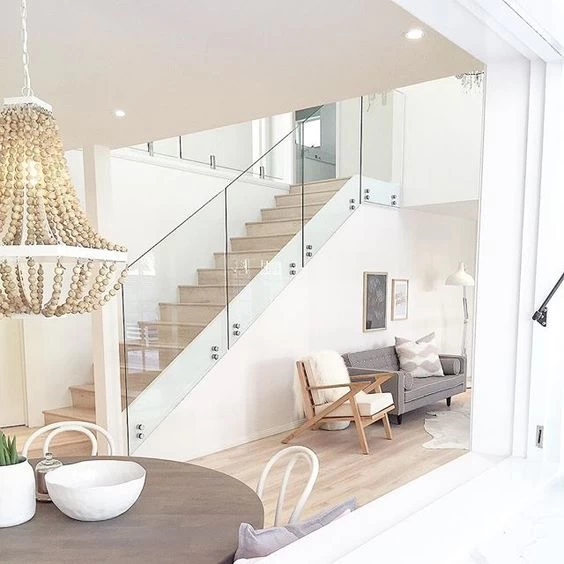
However, there are common challenges that can potentially stand in the way of glass railing installations – but this does not need to be the case. Here are four common challenges when working with glass railing installations and strategies to help glaziers overcome them.
Lengthy preparation time
Glaziers that have worked with glass railings know the challenges of traditional panel setting. Tempered glass is placed into a heavy-base, aluminum shoe, then set in place with a wet-glaze medium such as anchor cement. While structurally sound, the installation process is time consuming and messy. This traditional method for setting glass includes time-intensive steps from mixing the cement filler to monitoring and reapplication. This meant the glazier had to pour the cement filler, wait for the cement to cure and then repeat as needed.
When working with product specifications or specifications that allow for product equivalents (“or-equal”), consider locking mechanisms that eliminate the need for wet-glaze and the associated setting issues. Dry-glaze locking mechanisms are unlike wet-glaze panel installation in that clamps are used to hold the glass in place and later adjusted and tweaked for other hardware installation. Dry-glaze also employs advanced locking mechanism technology that alleviates the tasks of sealing, setting blocks, mixing and administering multiple pours of cement then waiting for the cement to cure – saving the glazier valuable time.
On-site fabrication
Railings have always been considered a product installed by miscellaneous metal fabricators. Many glaziers have avoided becoming involved in the metal aspect of railing systems as they don’t fabricate metal nor have all the tools for an installation of a metal railing system. As such, they stay away from railing projects resulting in lost revenue opportunities. It’s understandable considering railing projects have traditionally required a range of fabrication skills such as bending, welding, and finishing. However, fabrication isn’t necessarily a requirement anymore.
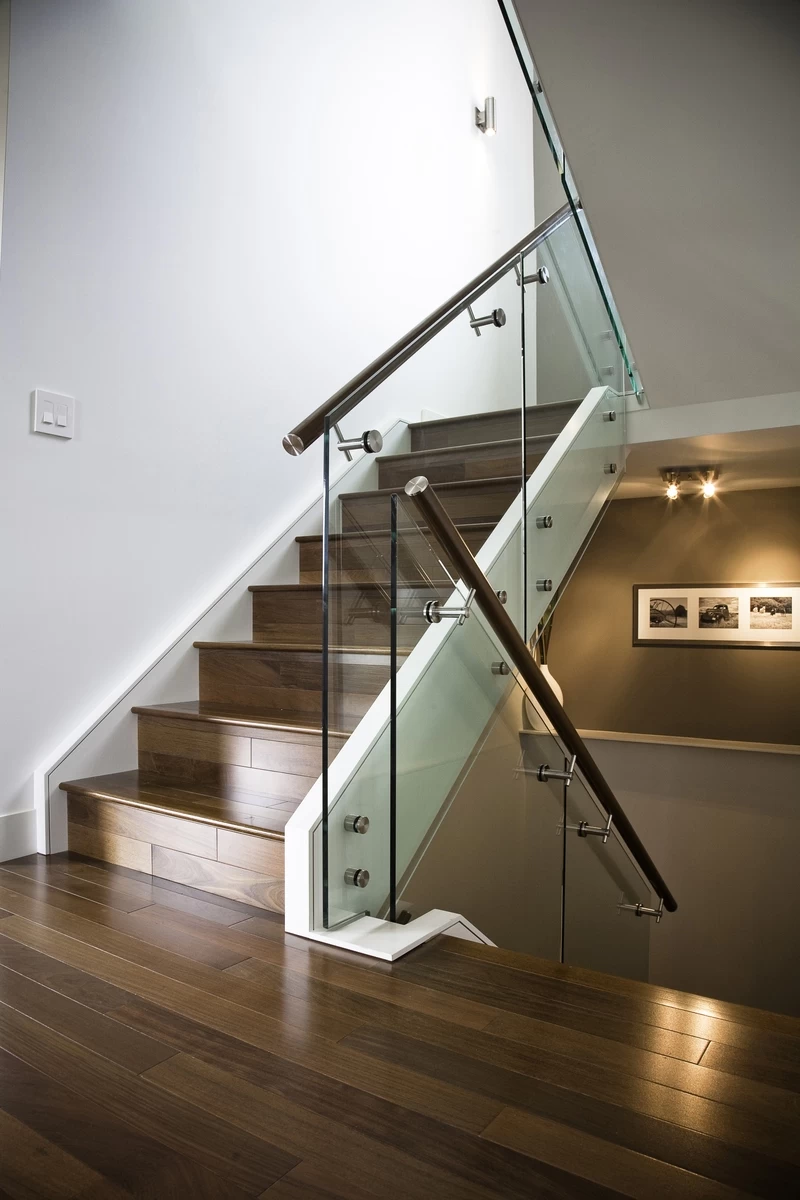
As railing systems have evolved, components for glass railings have evolved as well to simplify installation and mitigate fabrication steps. When specification allows for equivalent products, look for product solutions that offer non-weld, mechanically assembled railing systems to allow for faster, simpler installation without any tools or training. This will minimize the challenges that come with fabrication.
Meeting safety requirements
Growing code compliance, higher glass performance requirements, and trends for improved sight lines all place a greater emphasis on safety. Broadly speaking, when it comes to specification and installation it is the glaziers’ duty to understand which code to follow based upon the specific application of their project and local standards. Codes tend to evolve frequently and vary by jurisdiction. This challenges glaziers to stay on top of the varying regulations and ensure each job is properly specified and installed.
Allow yourself to get grounded on the most important standard requirements for railings. Additionally, consult the experts and local authorities having jurisdiction for each installation. A working knowledge of the most important standard requirements for railings and implications should include height, spacing and load bearing (keeping in mind that local code may vary). In most residential applications, the guard height must be a minimum of 36 inches. In commercial applications, the guard height must be a minimum of 42 inches. No opening in the guard is permitted that would allow the passage of a four-inch sphere. This four-inch sphere rule is a key reason why glass railings have been a popular choice for guard applications, as they meet the opening limitation and provide an unobstructed view. The system must meet a concentrated load of 200 pounds or a uniform load of 50 pounds per square foot. When selecting a glass railing system, make sure to acquire the test data from the supplier.
When consulting product experts, use the supplier as a guide for installation techniques. This ensures you obtain exacting specs and drawings to simplify the process. It also helps to have a clear assessment of building use, application, geographical concerns and all that effects the specified glass railing system and installation. Also, consult with the local building authority. Building codes and standards register hundreds of pages across a range of building requirements. They are updated constantly and the local authority will confirm local requirements and interpretations.
Selecting the right glass
It’s not only the railing components of a system that have evolved with regulation. Code requirements have also shifted and added challenges for glaziers in glass selection. Tempered, laminated glass is now required in the U.S. following the introduction of the IBC 2015 building codes. In Canada, requirements vary across provincial and municipal boundaries. National standards call for glass labeled as safety glass under CAN/CGSB-12.1-M90, which would require either tempered, laminated or tempered and laminated panel. Additionally, whether a minimally supported or base shoe railing system, the shift to laminated glass focuses on edge quality and the desire to achieve the same consistency and appearance of monolithic glass. As such, glaziers must think about both appearance and function.
At a minimum ensure the laminated glass complies with standard quality criteria. Additionally, due consideration should also be given to the quality of the laminated glass’ exposed edges. Different qualities of glass produce different tolerances, and as a result can be damaged when being moved around a job site or at installation. Make sure you know the source of your glass selection. A good producer will produce test data for quality and performance of the sheets you’ve ordered.
Don’t let challenges get in the way of opportunity
With the use of glass trending up with the rise in daylighting, it is becoming increasingly common to adopt glass railing systems into the mix. Glaziers not working with glass are missing out. Fortunately, new systems, solutions and techniques are being designed to take away many of the more challenging and time-consuming aspects of the job. As importantly, resources are out there to help ensure a successful install. Your supplier as a resource can guide in selecting and working with the right material, and serve as a resource for questions to match each job for a given installation. As the design world continues to let the light in with glass, you no longer have to let the challenges stop you from getting the most out of glass.
Tips and tricks
Here are additional tips to keep top of mind to minimize potential installation challenges.
Attachment to substrate
When installing glass railings, attachment to the substrate is central to the success of your glass railing installation. All loads placed on the top of the guard are exponentially transferred to the base connection. Test data you receive from your supplier will have specific recommendations as to what surfaces and means of attachment are acceptable.
Vertical plumb
In particular, when using dry-glaze glass rail systems, make sure your base shoe is properly plumbed as the mechanism will force the glass to follow the vertical line of the shoe. Take the time to plumb the shoe and you will avoid problems with the glass installation.
Top rail
It is not uncommon to see glass railing without a top rail. This should be avoided. The only allowance now for a glass railing without a top rail is when using laminated tempered glass and permission is obtained from the local inspector.
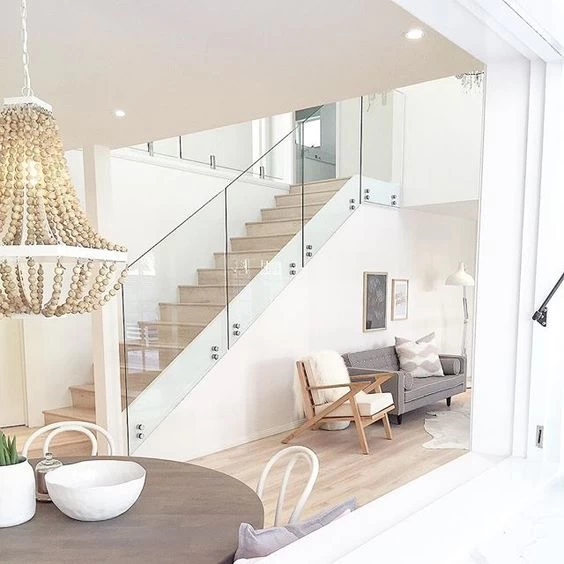
However, there are common challenges that can potentially stand in the way of glass railing installations – but this does not need to be the case. Here are four common challenges when working with glass railing installations and strategies to help glaziers overcome them.
Lengthy preparation time
Glaziers that have worked with glass railings know the challenges of traditional panel setting. Tempered glass is placed into a heavy-base, aluminum shoe, then set in place with a wet-glaze medium such as anchor cement. While structurally sound, the installation process is time consuming and messy. This traditional method for setting glass includes time-intensive steps from mixing the cement filler to monitoring and reapplication. This meant the glazier had to pour the cement filler, wait for the cement to cure and then repeat as needed.
When working with product specifications or specifications that allow for product equivalents (“or-equal”), consider locking mechanisms that eliminate the need for wet-glaze and the associated setting issues. Dry-glaze locking mechanisms are unlike wet-glaze panel installation in that clamps are used to hold the glass in place and later adjusted and tweaked for other hardware installation. Dry-glaze also employs advanced locking mechanism technology that alleviates the tasks of sealing, setting blocks, mixing and administering multiple pours of cement then waiting for the cement to cure – saving the glazier valuable time.
On-site fabrication
Railings have always been considered a product installed by miscellaneous metal fabricators. Many glaziers have avoided becoming involved in the metal aspect of railing systems as they don’t fabricate metal nor have all the tools for an installation of a metal railing system. As such, they stay away from railing projects resulting in lost revenue opportunities. It’s understandable considering railing projects have traditionally required a range of fabrication skills such as bending, welding, and finishing. However, fabrication isn’t necessarily a requirement anymore.
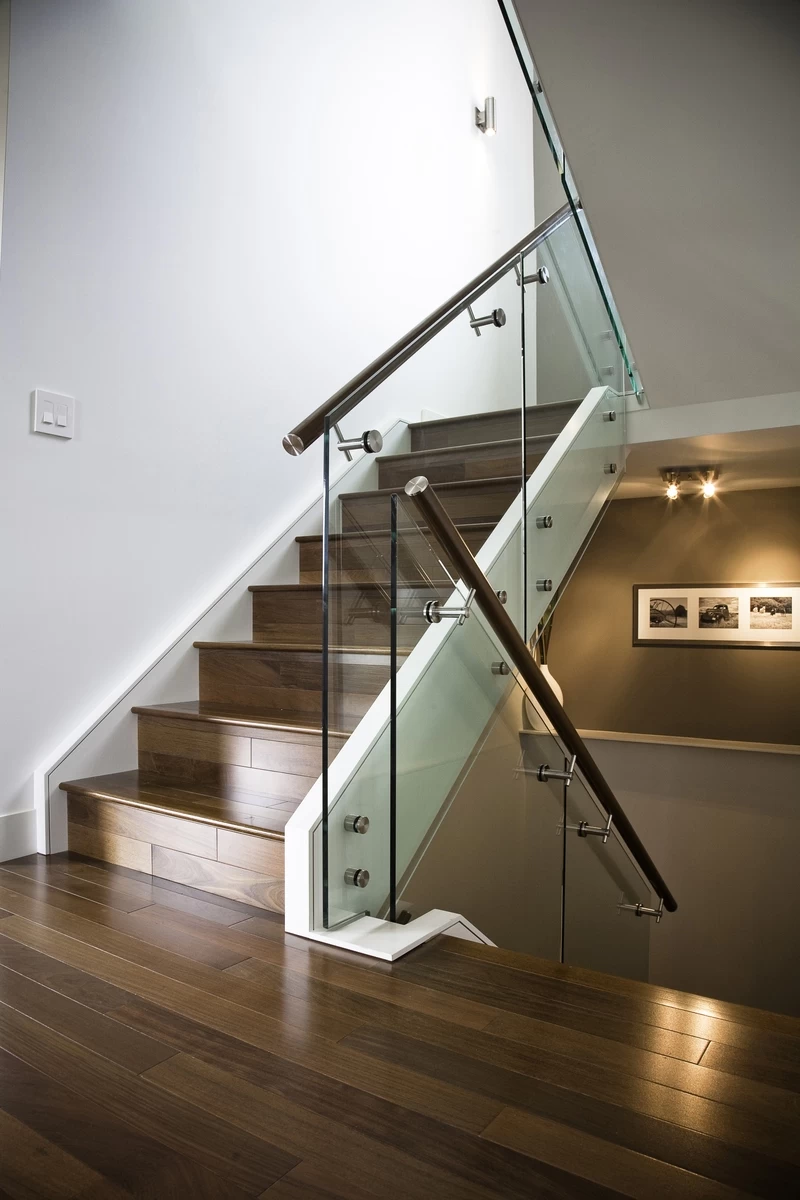
As railing systems have evolved, components for glass railings have evolved as well to simplify installation and mitigate fabrication steps. When specification allows for equivalent products, look for product solutions that offer non-weld, mechanically assembled railing systems to allow for faster, simpler installation without any tools or training. This will minimize the challenges that come with fabrication.
Meeting safety requirements
Growing code compliance, higher glass performance requirements, and trends for improved sight lines all place a greater emphasis on safety. Broadly speaking, when it comes to specification and installation it is the glaziers’ duty to understand which code to follow based upon the specific application of their project and local standards. Codes tend to evolve frequently and vary by jurisdiction. This challenges glaziers to stay on top of the varying regulations and ensure each job is properly specified and installed.
Allow yourself to get grounded on the most important standard requirements for railings. Additionally, consult the experts and local authorities having jurisdiction for each installation. A working knowledge of the most important standard requirements for railings and implications should include height, spacing and load bearing (keeping in mind that local code may vary). In most residential applications, the guard height must be a minimum of 36 inches. In commercial applications, the guard height must be a minimum of 42 inches. No opening in the guard is permitted that would allow the passage of a four-inch sphere. This four-inch sphere rule is a key reason why glass railings have been a popular choice for guard applications, as they meet the opening limitation and provide an unobstructed view. The system must meet a concentrated load of 200 pounds or a uniform load of 50 pounds per square foot. When selecting a glass railing system, make sure to acquire the test data from the supplier.
When consulting product experts, use the supplier as a guide for installation techniques. This ensures you obtain exacting specs and drawings to simplify the process. It also helps to have a clear assessment of building use, application, geographical concerns and all that effects the specified glass railing system and installation. Also, consult with the local building authority. Building codes and standards register hundreds of pages across a range of building requirements. They are updated constantly and the local authority will confirm local requirements and interpretations.
Selecting the right glass
It’s not only the railing components of a system that have evolved with regulation. Code requirements have also shifted and added challenges for glaziers in glass selection. Tempered, laminated glass is now required in the U.S. following the introduction of the IBC 2015 building codes. In Canada, requirements vary across provincial and municipal boundaries. National standards call for glass labeled as safety glass under CAN/CGSB-12.1-M90, which would require either tempered, laminated or tempered and laminated panel. Additionally, whether a minimally supported or base shoe railing system, the shift to laminated glass focuses on edge quality and the desire to achieve the same consistency and appearance of monolithic glass. As such, glaziers must think about both appearance and function.
At a minimum ensure the laminated glass complies with standard quality criteria. Additionally, due consideration should also be given to the quality of the laminated glass’ exposed edges. Different qualities of glass produce different tolerances, and as a result can be damaged when being moved around a job site or at installation. Make sure you know the source of your glass selection. A good producer will produce test data for quality and performance of the sheets you’ve ordered.
Don’t let challenges get in the way of opportunity
With the use of glass trending up with the rise in daylighting, it is becoming increasingly common to adopt glass railing systems into the mix. Glaziers not working with glass are missing out. Fortunately, new systems, solutions and techniques are being designed to take away many of the more challenging and time-consuming aspects of the job. As importantly, resources are out there to help ensure a successful install. Your supplier as a resource can guide in selecting and working with the right material, and serve as a resource for questions to match each job for a given installation. As the design world continues to let the light in with glass, you no longer have to let the challenges stop you from getting the most out of glass.
Tips and tricks
Here are additional tips to keep top of mind to minimize potential installation challenges.
Attachment to substrate
When installing glass railings, attachment to the substrate is central to the success of your glass railing installation. All loads placed on the top of the guard are exponentially transferred to the base connection. Test data you receive from your supplier will have specific recommendations as to what surfaces and means of attachment are acceptable.
Vertical plumb
In particular, when using dry-glaze glass rail systems, make sure your base shoe is properly plumbed as the mechanism will force the glass to follow the vertical line of the shoe. Take the time to plumb the shoe and you will avoid problems with the glass installation.
Top rail
It is not uncommon to see glass railing without a top rail. This should be avoided. The only allowance now for a glass railing without a top rail is when using laminated tempered glass and permission is obtained from the local inspector.